Soldering iron is a handheld tool for soldering, i.e. for joining two metal objects permanently, using a different metal (solder), which has a lower melting point than the components that are being joined. Soldering is the basic method of assembling electronic components on printed circuit boards.
Choosing a soldering iron for an electronic workshop is a very important step in organizing this place. Many beginner electronic engineers may wonder which soldering iron will work for them, and therefore, how to pick the best soldering iron. There are many solutions available on the market, and whether you need a simple soldering iron, soldering gun, or something more advanced, e.g. a soldering station depends on your individual needs.
If you are an amateur and you are just starting your adventure with soldering, check out the following tips.
First of all, you have to choose between a simple soldering iron (often described as a soldering pencil) and a soldering gun equipped with a transformer. There are also hot air soldering irons, but they are designed for advanced users and are used mainly for soldering SMDs (surface mounted devices), especially including large integrated circuits with connectors located on the bottom surface (e.g. BGA, QFN).
You should keep in mind that soldering guns heat up faster than soldering pencils, but if you need a more precise tool, choose the latter. They are available with much smaller soldering tips that are ideal for soldering small parts – that is why such tips are sometimes called “needle” tips.
There is a number of important parameters of a soldering iron for electronics that should be taken into consideration when choosing this tool – power, operating temperature range, soldering tip size. Their selection depends on the intended purpose of the soldering iron – you should consider it before making your final choice.
In this article, you’ll learn about:
Picking a soldering iron and its intended purpose
When picking a soldering iron for electronics, you need to know what its intended purpose will be. You will need a different soldering iron for soldering cables than for working with SMD components.
If the soldering iron you are looking for is to be used for soldering wires, especially those with a larger cross-section, then it is best to choose a tool with high power – (over 100 W) and a large soldering tip. For this purpose, soldering guns and simple soldering irons are a perfect solution.
For soldering larger electronic components, especially those used for THT mounting (i.e. with pins), you can choose a soldering gun or a soldering pencil. If you choose a soldering gun, you will need the right tip for it.
For soldering small electronic components, especially SMDs, you will need a soldering pencil equipped with a precise soldering tip.
Power and operating temperature range
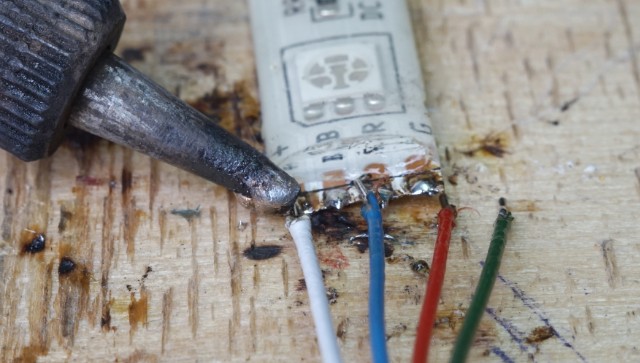
A soldering iron needs enough power to heat the workpieces to a certain melting point of the applied solder. Tin, used in electronics as a solder, melts at temperatures from approx. 180°C to 230°C – depending on the alloy additives. Lower temperatures are reserved for alloys containing lead that are currently being replaced (according to the RoHS Directive, from 1 July 2006, with certain exceptions, solder cannot contain lead). Lead-free solders melt in a temperature range from approx. 210°C to 230°C. This means that your soldering iron must heat the component to at least this temperature.
During soldering, the soldering tip of the soldering iron must be heated to a temperature that is much greater than the melting point of the solder in order to quickly heat the workpiece. Typical working tip temperature ranges from 260°C to 350°C and depends on the size of the soldering tip and the thermal capacity of the workpieces.
Not all soldering irons are fitted with a thermostat – it is worth making sure that the tool you buy is capable of maintaining a constant temperature of the tip. This is particularly important when soldering sensitive electronic components, because overheating can damage them.
In the case of soldering or tin plating (so called tinning) of thick cables, you will need a lot of power to quickly heat up a large volume of metal in the cable. Soldering irons with a power of more than 100 W and soldering guns equipped with a transformer are suitable for this purpose. For soldering electronic components, you should use a precise soldering pencil with a power ranging from 30 W to 90 W. It must be equipped with a precise temperature control system in order not to damage the soldered components.
More powerful soldering irons heat up faster and maintain the desired temperature more steadily. If the purchased tool has a good temperature control system, it is better to choose a model with a higher power, because it will significantly improve the comfort of use.
Soldering tip type and shape
Soldering tip – the hot element at the end of the soldering iron – is a part of the iron which is responsible for transferring thermal energy to the soldered workpiece. Being the most “industrious” part of the soldering iron, it wears-off pretty quickly. When buying a soldering iron, make sure that the matching soldering tips are easy to buy and replace. In this way, in the event of damage to this component, it will be possible to replace it without any problems.
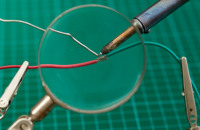
Soldering tips are available in various sizes and shapes. The most popular are chisel, minispoon, hoof and conical tips. Remember that when choosing a soldering tip, apart from its shape, you should also pay attention to the compatibility with your soldering station.
The size of the soldering tip should be matched to the soldered element – the larger the soldered element, the bigger the soldering tip should be to transfer heat more effectively. The shape of the tip, in turn, affects the distribution of the solder on the soldered surface – minispoon is the most versatile and recommended choice for beginners.
Ergonomics
When choosing a soldering iron, you should also pay attention to the shape of the handle. A comfortable soldering iron will give us greater operating comfort, so it is advisable to buy a device fitted with e.g. silicon overlays on the handle. If you prefer a gun grip, characteristic of soldering guns, but need a simple soldering iron with a precise tip, consider choosing e.g. JBC TOOLS 55N.
Accessories
Quite often soldering irons are provided with auxiliary accessories. While this should not dictate the choice of the device itself, it is good to make sure that the purchased set includes a stable stand on which you can place the soldering iron and a tip cleaner – with metal chips or a sponge. You can also purchase them separately.
Cordless soldering irons
Cordless soldering irons are becoming more and more popular. Until recently, this area was dominated by gas soldering irons, but nowadays more and more battery-powered electrical appliances of this kind are appearing on the market.
Cordless soldering irons are an ideal solution if you have some fieldwork to do, in places with no access to an electrical outlet. It is good to have such a soldering iron with you even in a tent, on a camping site or in a box with basic tools in a car.
Picking a soldering iron is just the beginning!
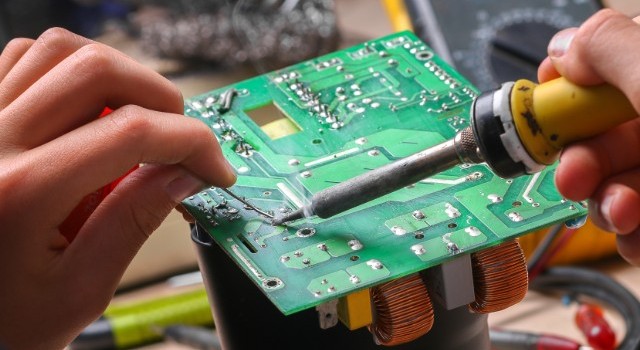
When you buy your first soldering iron, you should also equip yourself with a range of basic accessories and materials needed for soldering or maintaining your new tool in working order.
First of all, you need a solder and flux. Solders are usually available in the form of wire of various diameters. You should select it according to the size of the soldered elements – for soldering small SMD elements a wire with a diameter of 0.25 mm or 0.3 mm should be a perfect choice. For tinning of the ends of thick wires it is worth choosing 3 mm or 4 mm solder wire.
When it comes to solders, choose lead-free ones. They have a higher melting point and worse bonding properties than solders containing lead (which are not used anymore), but they are not as harmful to health and the environment as lead alloys. Nevertheless, remember to work in a well-ventilated room and use e.g. special fume extractor.
The flux facilitates the melting of the solder and prevents its oxidation. In amateur applications, rosin is still the most widely applied flux. It is available in many forms – paste, solution or a classic, solid form. In addition, there are other fluxes available in the form of pastes, pens, gel, etc. It is also worth choosing "No Clean" fluxes, i.e. fluxes which don’t cause PCB corrosion and don’t require washing the PCB after soldering. If you have already purchased a flux that requires washing, you should read its description – check whether it should be washed with water or other agents, such as isopropyl alcohol.
In terms of soldering chemicals, in addition to fluxes and PCB cleaners, a tip regeneration agent may also be useful for cleaning solder residues on PCBs. It restores the fresh look of even the most damaged and worn tips. It should not be used regularly, as it cannot replace taking good care of the tip – i.e. regular cleaning it with a metal sponge and not overheating it unnecessarily.
In addition to the above soldering accessories, you’ll surely need a desoldering pump to remove excess melted binder, and also tweezers or a vacuum pick&place device for integrated circuits that will help you grip hot electronic components while soldering.